- Asia Pacific News
- Europe News
- Municipal Solutions
- North America News
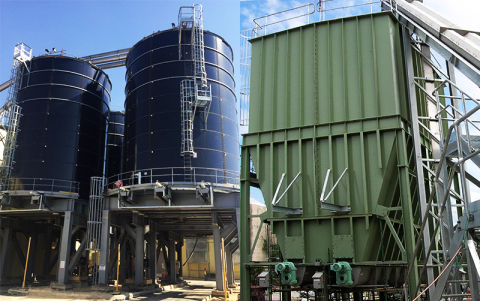
It is important to understand the variations in silo outloading technology, and which system is right for each type of facility. The most significant difference lies in the outloading methods for non-free-flowing materials, with sliding-frame silos and live-bottom silos being the two main and distinct outloading options for this kind of material.
Available in a rectangular and round silo configuration. The Sliding-Frame Silo is designed to reduce bulk material buildup that can cause potential blockages at the bottom of the silo. A hydraulically powered frame is designed to break up any "bridges" - collected material that can gather and solidify over the extraction screw - and help move the material toward a discharge point in the silo.
An effective choice for facilities that frequently handle non-free-flowing materials, including solid waste, wood chips and dewatered sludge The sliding-frame silos from SPIRAC features a simple operation with few moving parts. That means your maintenance concerns should be minimised, the operation is exceptionally reliable and power consumption remains low.
For facilities that regularly handle the most challenging sticky materials, Live-Bottom silos may be a more suitable option. The wastewater industry, in particular, may find these devices to be effective - in fact, they're custom-designed with storage, transfer and outloading of dewatered sludge in mind. Unlike the Sliding-Frame Silo, a Live-Bottom features multiple spiral screws - usually from two to eight depending on the size and intended use. Running side-by-side, the movement of the screws ensures material bridges, and blockages are unable to form.
A combination of factors needs to be considered when deciding which outloading silo system is the most suitable for your facility.
The Sliding-Frame silo is considered a compact setup and requires less space than a Live Bottom silo with the same capacity. If you are looking for a round silo, a sliding frame is most likely the preferred option. Round Live-Bottom Silos are only suitable for 3m to 4m diameter silos. The round live-bottom silo needs to be tapered at the silo floor and fit to a rectangular Live-Bottom solution. The sliding frame silo uses a flat floor and does not require tapered walls, making it more cost-efficient if space is at a premium.
If you have height restrictions a sliding frame set-up might be the best solution for you. Live bottom silos need tapered walls which decrease the storage capacity. Depending on your requirements the most cost-effective solution is going to vary. For a long and skinny rectangular silo, a Life-Bottom silo is the most cost-efficient solution. If you are looking for a large round silo you should consider a round sliding frame silo.
If you are dealing with a corrosive material or if the location of your storage silo is close to the coast a sliding frame will most likely be the better option. When you are dealing with sludge with a high salt water content or if the silo is placed close to the coast corrosion is a sliding frame set-up should. A live bottom silo is going to require welded reinforcement at the bottom of the silo which will corrode faster than a sliding frame silo. Especially if we are using bolted fused glass coating panels to create a round sliding-frame silo.
Similar to the Sliding-Frame, Live-Bottom Silos run at a very low RPM, ensuring minimum wear and maintenance is required. Through normal operation, an inspection of the units should only be required every 5-10 years, with the components themselves lasting as long as 20 years.
Our silos and tanks - both sliding-frame and live-bottom - are available in small (40 m3) and large storage capacities (1000m3), the silos can be manufactured in high-spec mild steel, Glass-Fused-to-Steel or stainless steel. Given the nature of their use, corrosion protection is also a feature, with a range of specifications available to suit many industries. Need to know more about silos, tanks and outloading methods?
Is your material handling system in need of storage equipment? For more information about the best silo solution for your facility, speak to SPIRAC today.