- Europe News
- Municipal Solutions
- Shaftless Spiral Conveyors
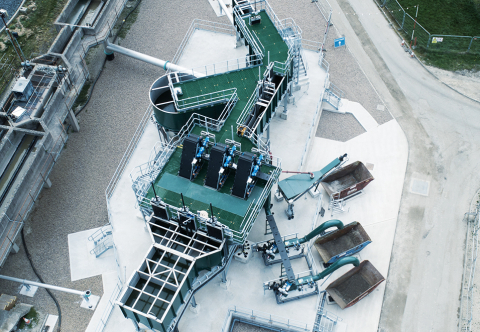
A pre-fabricated treatment plant package, constructed offsite, has enabled a water company in northern England to implement much-needed improvements to its inlet works while keeping its carbon footprint to a minimum.
We designed and built three of our reliable FINEGUARDTM screens at our manufacturing plant for the Wastewater Treatment Plant serving a population of 25,000. This approach minimized the need for civil engineering work and eliminated on-site concrete pouring.
Our innovative treatment system is positioned on a robust precast concrete foundation, supported by a galvanized steel structure elevated 5m above ground level. This design facilitates the smooth flow of wastewater to downstream process units.
Before this installation, the inlet struggled to handle the incoming volumes, leading to the constant bypassing of debris through the old screens into the secondary treatment area.
As part of a £12.3M upgrade initiative, the new treatment process has already yielded significant improvements in the water quality discharged into the local river. Ammonia discharge levels, previously at 13mg/l, have now been reduced to a mere 0.1mg/l.
Each of our three FINEGUARDTM screens can handle a maximum flow of 566 l/s of sewage at a designed water depth of 1m downstream. These screens consist of perforated panels attached to drive chains on both sides. A self-adjusting brush mechanism with water spray jets cleans the screen panels of debris as they reach the discharge section, ensuring optimal performance. The screen panels are secured for easy replacement of individual units with minimal effort and downtime.
Screenings are conveyed from the screens via a launder trough system, and our SPIROWASH® units subsequently wash out organic material, reducing the volume and weight of the screenings through compaction before delivering them to a skip via a press tube.
Additionally, a grit vortex unit effectively removes suspended grit from the sewage flow. This unit includes a pre-fabricated grit vortex chamber capable of handling up to a maximum of 628 l/sec of screened raw sewage flow. The extracted grit is conveyed by a grit pump to our SANDSEP® grit separator unit, which can handle up to 20 l/sec of grit slurry. The SANDSEP® unit dewaters and discharges the grit into a skip.
We emphasize the growing demand from water companies and Tier One contractors for comprehensive packages that minimize on-site time and reduce the use of civil engineering materials, particularly concrete. We also highlight the cost-saving advantages of offsite construction, testing, and wiring for wastewater projects.